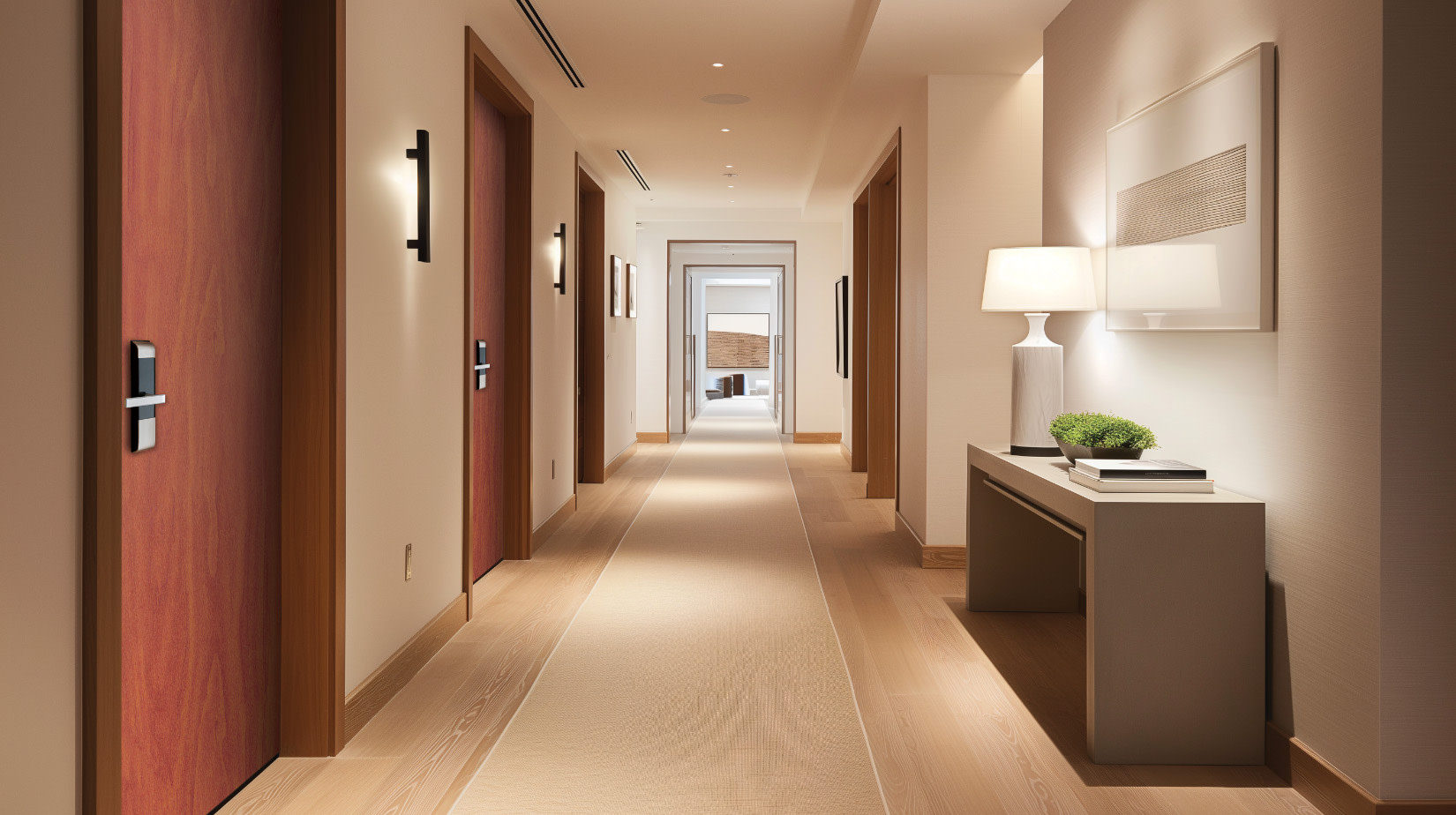
HPDL Doors Explained: A Durable and Cost-Effective Solution for Any Project
Decorative laminate is a versatile material widely used in both residential and commercial architecture, thanks to its durability, cost-effectiveness, and the extensive range of finishes available. When it comes to doors, high-pressure decorative laminate (HPDL) offers a perfect balance between functionality and design. This post will explore the manufacturing process of HPDL, as well as its benefits, construction, and practical applications in modern building projects.
What Is Decorative Laminate?
Decorative laminate consists of thin sheets of material that are applied to surfaces such as doors, walls, furniture, and countertops for both protective and aesthetic purposes. Laminate sheets can mimic the appearance of wood, stone, or other natural materials, while also providing protection against wear and tear. There are two main types of decorative laminate: low-pressure decorative laminate (LPDL) and high-pressure decorative laminate (HPDL). Both have unique properties and are suited to different applications.
HPDL vs. LPDL: What’s the Difference?
Low-Pressure Decorative Laminate (LPDL) is formed using lower pressure (600 psi) and heat (around 390°F), making it flexible and impact-resistant. LPDL is mainly used in high-traffic areas like flooring, where its softer construction can better withstand impacts without cracking or chipping.
High-Pressure Decorative Laminate (HPDL), on the other hand, is constructed under high pressure (about 1,400 psi) with slightly lower temperatures. This results in a stiffer and more durable material, suitable for doors, walls, countertops, and furniture. HPDL sheets offer a wider range of textures and finishes than LPDL, making them a versatile choice for design-oriented projects.
The Manufacturing Process of HPDL
HPDL is created by pressing together multiple layers of material using heat and high pressure. This process ensures the laminate is dense, durable, and capable of withstanding wear, scratches, and stains. Here’s how HPDL is made:
1. Kraft Paper Layers: The base of HPDL is made up of multiple layers of kraft paper, which are infused with phenolic resin to increase durability and impact resistance. The number of layers creates the thickness and strength of the final HPDL sheet.
2. Decorative Layer: On top of the kraft paper, a high-grade decorative paper is applied. This paper features the chosen design, whether it’s a solid color, wood grain pattern, or other colors and patterns.
3. Clear Overlay: The topmost layer is a transparent melamine overlay that protects the decorative sheet from wear, scratches, and damage from chemicals.
The layers are placed in a press, where heat and pressure cause the resins to cure and bond the layers together. Steel plates give the surface its final texture or sheen, allowing for finishes that range from smooth to highly textured. HPDL sheets typically range from 0.028” to 0.048” thick, with door-grade sheets falling on the thicker end of this spectrum.
How HPDL Doors Are Made
The process of making HPDL doors is similar to the construction of wood veneer doors, combining HPDL sheets with a solid core, stiles and rails, crossband, and edge bands.
• 5-Ply Construction: HPDL doors are typically 5-ply, meaning they consist of five layers:
1. Two HPDL sheets (one on each side of the door).2. Two layers of high-density fiberboard (HDF) crossband, which helps prevent telegraphing and warping due to temperature and humidity changes.
3. A solid core, which can be made from particleboard or structural composite lumber, depending on the door’s intended use. Hollow core construction is not recommended.
Core Options for HPDL Doors
HPDL doors can be constructed with various core options, depending on the specific needs of the space or project. Some of the most common core options include:
• Particleboard Core: A popular and cost-effective choice that provides solid structural support.
• Extra Heavy-Duty Particleboard Core: Adds enhanced durability and resistance to impact, making it suitable for high-traffic areas.
• Structural Composite Lumber Core: Provides superior strength and longevity, ideal for areas where durability is a priority.
• Fire-Rated and Acoustic-Rated Cores: These specialized cores offer additional benefits, such as fire ratings up to 90 minutes to meet life safety codes or soundproofing, and will be covered in more detail in subsequent discussions.
Why Choose HPDL Doors?
HPDL doors offer several advantages that make them a popular choice in commercial projects:
• Durability: The high-pressure manufacturing process makes HPDL doors resistant to scratches, wear resistance, and impacts, making them ideal for high-traffic areas.
• Design Flexibility: HPDL is available in a wide range of colors, patterns, and textures, giving designers the freedom to create spaces that are both functional and visually appealing.
• Low Maintenance: HPDL surfaces are easy to clean and maintain, ensuring they stay looking great for years.
Final Thoughts
High-pressure decorative laminate (HPDL) is an excellent choice for creating durable, aesthetically pleasing doors that can stand up to the demands of commercial spaces.Understanding the manufacturing process, construction techniques, and core options available for HPDL doors can help you make informed decisions for your next project.